CUSTOMER: AMTROL
Challenges: As part of its manufacturing process, AMTROL needs to properly process its waste. This begins by collecting metal particulates to separate oils and neutralize caustic components. AODD pumps then transfer the resulting sludge for final processing by filter presses, which separate the ‘sludge cakes’ from clean water. Overall, the filter presses process up to 9,600 gallons of waste sludge per day and produce over 100 tons of sludge cakes each year; however, the older AODD technology was a limiting factor in realizing the filter presses’ full potential.
Goal: Upgrade to technology that could leverage, not hinder, their new filter presses and expand their waste-processing capacity without adding more equipment.
Why It Worked: By replacing aging technology with new Wilden Pro-Flo SHIFT ADS, AMTROL eliminated reliability issues, decreased pump maintenance, reduced water processing operating costs by 60%, and improved pump productivity by 40%. |
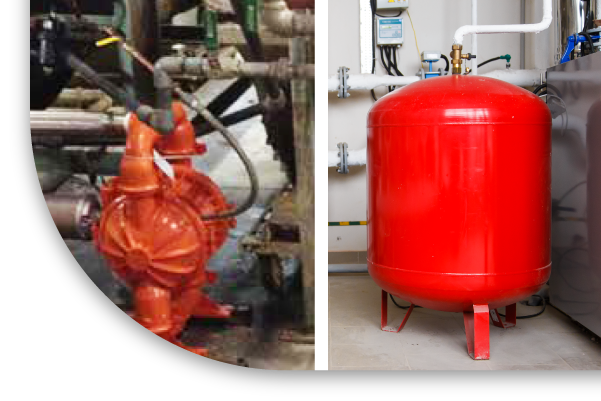 |